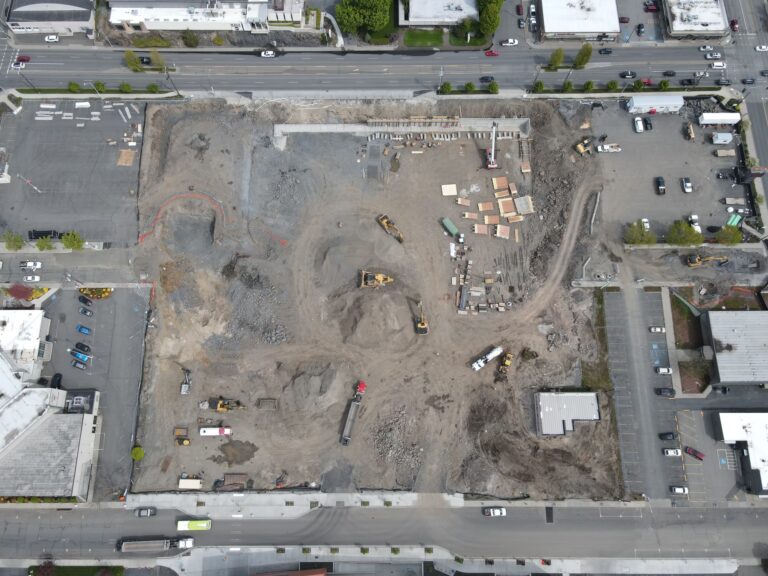
Quarry Drilling & Blasting
Our Bread and Butter
We utilize cutting-edge drone and GPS technology to measure, design, layout, and execute a drill and blast program. Working together with the client, we have made blast optimization one of our top priorities and we recognize it is a process that is never-ending. We have taken numerous clients from smaller diameter hole patterns to much more efficient blast designs, ultimately saving them hundreds of thousands of dollars annually without sacrificing fragmentation or crusher throughput. Every blast is video recorded via drone for safety and record keeping purposes.
Pre-split Blast Technique
Related Projects
Work With Us
With blast optimization, we have taken many clients from smaller diameter hole patterns to more efficient blast designs. This process has saved them money without sacrificing fragmentation or crusher throughput.
Equipment & Parts
We’ve relied on Furukawa Rock Drills USA to be our exclusive rock drill rig provider for over a decade. Our position as the authorized Furukawa Rock Drill dealer in the Pacific Northwest has allowed us to create an entire fleet of over 30 exclusively Furukawa drills.
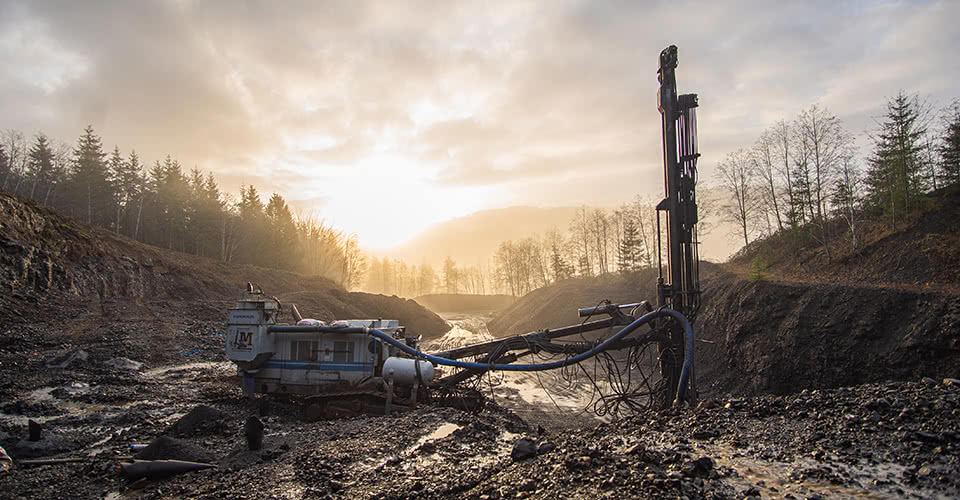
FAQs
Blasting is an essential part of our economy. Minerals, metallic ores, coals, and aggregates all are extracted from the earth. The first step in this process is blasting. These materials can be extremely hard and cannot be removed mechanically until fragmented and displaced.
No. We strictly adhere to standards that your state, the United States Bureau of Mines, and the Office of Surface Mining have determined to be safe blasting criteria. These standards are long proven and scientifically tested to keep structures safe from vibration.
Yes. Our company has many years of experience with technical blasting within close proximity of structures. We have skilled employees that use various forms of vibration prediction. We’ve completed projects within five feet of structures with no damage incurred.
The survey is an inspection, usually photographed and/or videotaped, of the structures to document conditions prior to blasting. This is a standard procedure that we employ prior to blasting commencement. An independent third party will survey structures located close to the blast area. If damage is suspected, the pre-blast survey company will check for discrepancies.
McCallum Rock Drilling has many seismographs and operators that measure vibration. Seismographs are calibrated annually by the manufacturer to ensure accuracy. All seismographs also have a self-check mode that runs prior to monitoring.
Yes, vibration and noise are inherent by-products of a blast, all of which can be controlled to minimize human perception. All blasts are carefully designed by professionals and results are predetermined.
We contact any local law enforcement, fire departments, and emergency response prior to blasting operations. In addition, we contact anyone within a 300 foot radius from a blasting operation. This is done verbally and/or by letter. This is standard for any project we do. Permits for blasting are also handled by McCallum Rock Drilling.
Rock hammering is slow, inefficient, costly, and has the same inherent properties of blasting on a smaller scale. Blasting can actually be quieter than rock hammering, and takes much less time. A typical blast duration is usually 1 to 3 seconds, while rock hammering can take over two weeks to displace the same amount of volume incurred by a single blast.
By definition, flyrock is debris that is propelled outside of the blast zone. Shot design, powder factor, stemming material, delay sequence, and blasting mats are all factors considered to control flyrock. Every blast we design and shoot uses proper principals for all applications to control flyrock.
Every project is different and duration is based on a number of factors. McCallum Rock Drilling has a large fleet of efficient and powerful drills and highly skilled and motivated employees to get every project completed in the safest, fastest and best manner possible.